A. |
General provisions. |
|
1. |
Starting with oxygen is strictly forbidden
(explosion danger). |
|
2. |
Follow the procedures when preparing, starting, running and stopping. |
|
3. |
No one should be in the longitudinal direction of the compressor
during operation in the event that its end caps should blow out. |
|
4. |
Make sure the compressor receives sufficient air at start and during
operation. |
|
5. |
Important: Note operating hours,
any comments and sign the the "operating hours form" (a
designated form which hangs in the Compressor Room). |
|
|
Use hearing protection at all
times in comp.room when operating the compressor. |
|
|
Only personnel with thorough
training can operate the compressor. |
B. |
Preparing to start. |
|
6. |
Open the vent valve (1) on the pressure sustaining valve, as
well as 1st (7) and 2nd (8) stage blowing taps. |
|
7. |
Place the hand crank on the fuel pump rectangular stud (2) and
crank the pistons apart to outer dead center (clockwise). |
|
8. |
Remove the hand crank. |
|
9. |
Close vent valve (1) on the pressure sustaining valve, and 1st
(7) and 2nd (8) stage blowing taps. |
|
10. |
Press the control spindle (4) of the fuel pump. |
|
11. |
Start Air: Open the valves for start
air and check that the reduction valve provides 35-45 kg/cm2. |
|
12. |
Open the valves for fuel and cooling water (cooling water comes
from the pressure line, the valve opens immediately after the compressor
has started). |
|
13. |
Check oil level (9) for lubricating oil (use only suitable compressor
oil). Turn lubrication oil drive shaft 6-8 times by hand. |
|
14. |
Open the valves on the water collector, check that vents to
the air dryer are open and allow air to enter the air board and further
to the air bank. |
C. |
Start |
|
15. |
Press start lever (6) clockwise and pump the fuel 2-3 times
with primer handle (5) when the gauge pressure of 1st stage is 2-3 kg/cm2. |
|
|
At 4-5 kg/cm2 at stage 1 and 26 to 28 kg/cm2
for stages 2, 3 and 4, disengage the stop knob (3) of the automatic
triggering switch and the compressor will start. |
|
16. |
After start: Check cooling water
(observe it at reference point II [check glass at cooler II]) and
check that the oil pump works (about 4-6 RPM). |
|
17. |
Shut off starting air. |
|
18. |
When the pressure on both towers of the air dryer is approximately
190 kg/cm2 it can be started by turning the switch
to I. |
|
|
If the dryer has undergone maintenance or repairs have been
carried out, the start procedure for the dryer should be followed.
Only technical officers are to perform this. |
|
|
Quick pressurization of the dryer could damage the drying substance. |
|
19. |
While operating: Every 5 minutes
make sure cooling water outlet temperature does not exceed 40°C
and the water pressure does not exceed 1 kg/cm2. |
|
|
Check that gauges behind the dryer area correct
(stage 1 5-7 kg/cm2, stage 2 9-12 kg/cm2). |
|
|
Check that the pressure on dryer pre filter does
not exceed 0.6 kg/cm2. |
|
|
Ensure that the gauges on the compressor are within
the allowable range (marked in a different color). |
|
|
Each 1/2 hour blow water from of the collector
and drain 1st stage blow tap (7) for oily sludge and water. |
|
|
Avoid the compressor stopping on its own (emergency stop) by performing
the steps under D when the pressure is 200 kg/cm2. |
D. |
Stop |
|
20. |
Turn the knob on the oil pump a few times. |
|
21. |
Raise lever (5) to the fuel container to stop the compressor. |
|
22. |
After stopping: shut off fuel and cooling
water. |
|
23. |
Turn off the air dryer by turning the switch to 0. |
|
24. |
Open air relief valve (1) on the pressure sustaining valve, and
lst (7) and 2nd (8) stage blow taps and blow water from the collector |
|
25. |
The safety valve has stopped the compressor:
Perform items 20 22, 23, 24. |
|
26. |
After compressor has cooled: Crank
the pistons back and forth two times. |
|
|
|
|
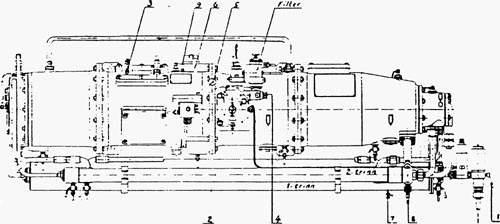 |
|
|
|
Note: |
For problems or questions contact: Soff.
TP or Clarification Leader. |
 |
 |
 |